CEMENT GRINDING PLANT & MACHINERIES

Our cement plant unit has continued focused on objectives of product improvement and quality. In our entire turnkey cement plant equipments and machinery, we supply a complete assembly consisting of different machines and equipment, which facilitate the plant to execute efficiently and manufacture a better-quality completed product as per the international quality standards. We are fully committed to combine our strengths with the best pricing structures. Cement plant machinery equipments used in cement plants are compact, powerful and reasonably priced that meet all applications, to give trouble free and competent performance. Unit has all the skills to commence all aspects of cement plant construction.
Clinker Grinding Unit
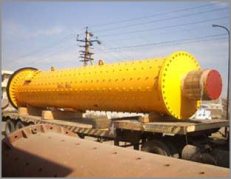
We supply a cement grinding unit. We supply grinding units upto 2000 TPD plants, capable of handling all types of cement. We offer to our clients a versatile grinding unit whose heavy and rugged construction is built for continuous trouble free operation everyday.We design and manufacture rust and moisture proof grinding units.
Kiln & Kiln Shells
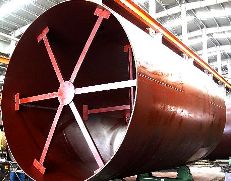
We supply all type of process equipments including Vertical and roller Kiln and Shells. Kiln Shells is involved in the process of burning the raw mixture thereby resulting in the clinker. This clinker is then subjected to grinding to produce cement. In modern cement manufacturing plants, kiln make the most complex and expensive portion of plant as it should be operated round the clock. Hence the duration till which kiln is active determines the output of whole plant. Pyroprocessing is the completely unique stage of the cement industry which is dedicated to the much specialized and complex multi-disciplinary technology.
Capacity Size & Application: Suitable for production capacity upto 10,000 MT per day.
Ball Mill
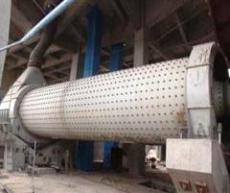
We supply ball mills for cement industry. We expertise in heavy fabrication with all latest equipped and technologies required for cement plants for up to 3000 TPD production. Ball Mill shell is fabricated from high quality tested plates. The mill consists, both side end bottoms (material steel casting) Girth gear, Mg. Steel liners bolted with heavy forged bolts & nuts, man holes, feed & discharge hood, torsion shaft, pinion with shaft, Pinion Bearing housing, cooling system and other machined equipments. Application: Common applications for our ball mills is grinding of clinker for cement manufacturing, mineral ore’s, calcium bauxites, silicates and other materials that can be ground into fines either by wet process or by dry process.
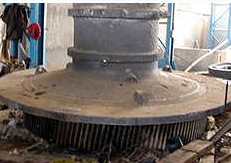
The mill headers are very useful in increasing the material temperature and that too in a perfectly continuous fashion particularly in heavy duty industry. The overall size of the kiln depends on the condition at which the process is going on. Depending on the specifications of the process, the length and diameter is calculated. Kiln sections will be sized depending on the practicability of the transport and efficiency of industry. The optimum capacity that will be compatible to ball mills is up to 5.0m diameter in shell. The size will be up to the flange diameter of 6.0 m and height is about 3.0 m. The max weight of single piece will be up to 50MT. These specifications will go well with the rod mills and ball mills.
Cement Mill Bearings
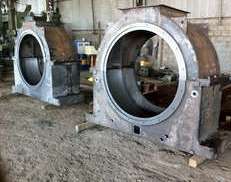
A bearing can be described as a machine element to check relative motion permitting desired motion and also reduces the friction between mobile parts. A bearing is designed to permit free linear form of movement or to execute free rotation in fixed axis. Manufacturing process of these bearings requires the usage of high-end current technology. The common form of motions that are acknowledged by the bearings are hinge motion (e.g. knee, elbow and door), spherical rotation (e.g. socket joint and ball), linear motion (e.g. drawer) and axial motion (e.g. shaft rotation).
Separators for Cement Plants
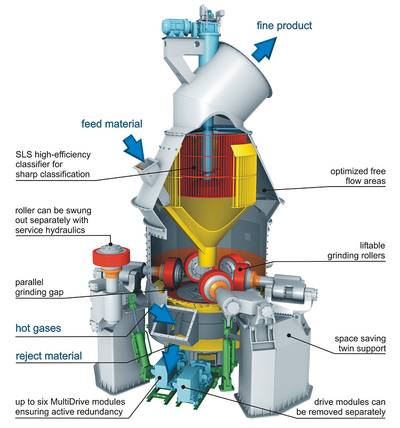
Basic function of this separator is to separate very fine sized particles from the coarse particles. During the separation process, the separated fine particles are collected at one end in the name of finished product whereas the coarse sized particles are further sent back to undergo the grinding process once again. A well efficient separator will always prevent the particles from overgrinding which on the other hand leads to wastage of energy. The separators can be classified into two types: the dynamic separators and the static separators.
Jaw Crusher Impact Crusher
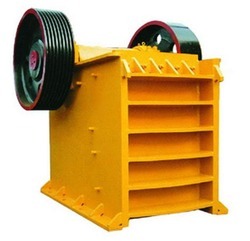
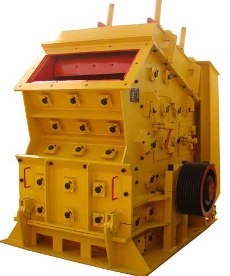